What is a Dosing Pump & How Does It Work?
There are many different types of pumps for use in fluid management.
One of those types of pump is called a dosing pump.
A dosing pump adds a set amount of liquid, such as a chemical or nutrient, to another liquid or process at regular intervals.
Dosing pumps are critical in applications where precise control over chemical delivery is essential.
This article will cover what a dosing pump is, how it works, its advantages and limitations, and possible alternatives to using dosing pumps.
Article Chapters
What is a Dosing Pump?
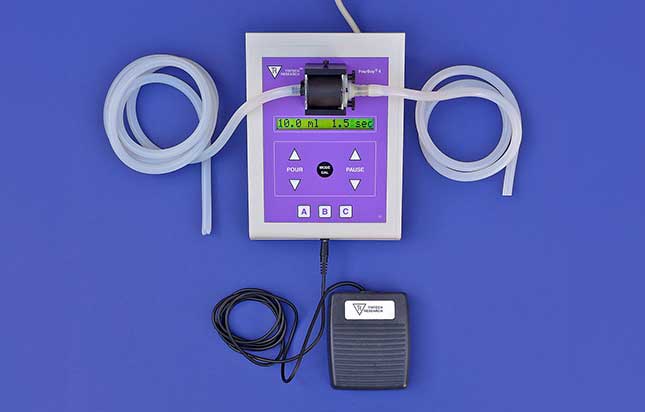
Source: Wikipedia
A dosing pump is a specialised pump designed to deliver precise amounts of liquid, typically chemicals or nutrients, into a process or system.
These pumps are essential in applications where exact dosing is crucial, such as water treatment, pharmaceuticals, food processing, and agriculture.
Dosing pumps can operate continuously or intermittently, providing flexibility in how and when the liquid is delivered.
They typically feature adjustable flow rates, allowing operators to control the amount of liquid dispensed accurately.
Many dosing pumps are automated, enabling remote monitoring and operation, which improves efficiency and reduces the need for manual intervention.
By ensuring precise chemical dosing, these pumps help maintain product quality, enhance safety, and minimise waste, making them an integral component in many industrial processes.
What is a Dosing Pump Used For?
Dosing pumps are versatile devices used across various industries to deliver precise amounts of liquids, typically chemicals or nutrients, into a system or process.
Their accuracy and reliability make them essential in applications where exact fluid dosing is critical.
Here are some of the primary uses of dosing pumps:
Water Treatment
Dosing pumps are essential in water treatment facilities, where they add disinfectants like chlorine to ensure the safety of drinking water.
They also help maintain proper pH levels by injecting pH adjusters, which prevent corrosion and scaling in pipes and storage tanks.
By ensuring precise chemical dosing, these pumps play a crucial role in producing clean and safe water for communities.
Agriculture
In agriculture, dosing pumps are used to deliver fertilisers, herbicides, and pesticides directly to irrigation systems.
This method allows for the targeted application of chemicals, optimising nutrient uptake by plants and minimising environmental impact.
By using dosing pumps, farmers can reduce chemical waste and improve crop yields while promoting sustainable farming practices.
Food and Beverage Industry
The food and beverage industry relies on dosing pumps to accurately measure and dispense additives, such as preservatives, flavouring agents, and colouring.
Consistent dosing is vital for maintaining product quality and adhering to regulatory standards.
Dosing pumps ensure that the correct amounts of these substances are added during production, helping to deliver safe and high-quality food products to consumers.
Pharmaceutical Manufacturing
In pharmaceutical manufacturing, dosing pumps are critical for accurately dispensing active ingredients into formulations.
Precision in dosing is essential to maintain the efficacy and safety of medications.
Dosing pumps also help streamline production processes, ensuring that the correct amounts are consistently used in each batch.
Chemical Processing
Dosing pumps are widely used in chemical processing industries to introduce various chemicals into production processes.
They ensure accurate ratios of ingredients, improving product consistency and quality.
Applications include manufacturing plastics, paints, and other chemical products where precise chemical dosing is crucial.
Cooling Towers and HVAC Systems
In cooling towers and HVAC systems, dosing pumps inject biocides, corrosion inhibitors, and other chemicals to maintain water quality and protect equipment.
This helps prevent harmful buildup, ensuring efficient operation and extending the lifespan of the systems.
How Does a Dosing Pump Work?
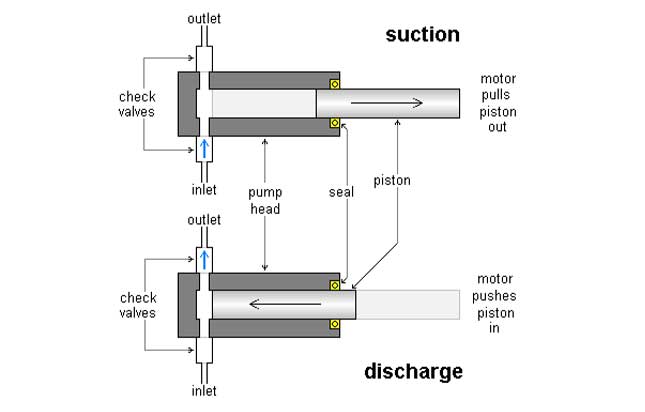
Source: Wikipedia
A dosing pump operates by moving a set amount of liquid with each stroke or rotation.
Here’s how it works in simple terms:
Fluid Intake
A dosing pump begins its operation by drawing fluid from a reservoir into its pumping chamber.
This is typically achieved through a suction valve that opens when the pump is activated.
The pump’s design ensures that the fluid enters smoothly, allowing for consistent dosing.
Metering
Once the pumping chamber is filled, the pump measures the amount of liquid present.
Many dosing pumps are equipped with sensors or controllers that help monitor the fluid volume accurately.
This metering process is crucial for ensuring the correct dosage is delivered in subsequent steps.
Dispensing
When the desired volume is reached, the pump activates a discharge valve, allowing the liquid to flow out of the chamber.
The fluid is then injected into the target system, such as a water treatment facility or agricultural irrigation system.
The dispensing can be set to occur continuously or at specific intervals, depending on the application requirements.
Repeat Cycle
After dispensing, the pump resets and begins the cycle again.
The suction valve closes, and the process of fluid intake, metering, and dispensing repeats.
This continuous cycle allows for precise and controlled delivery of liquids, making dosing pumps essential in applications that demand accuracy in fluid management.
What are the Different Types of Dosing Pump?
Dosing pumps come in various types, each suited for specific tasks.
The main types include:
Diaphragm Pumps
These pumps use a flexible diaphragm that moves back and forth, creating pressure to draw in and release liquid.
They’re highly accurate and handle chemicals well, making them ideal for water treatment and chemical processing.
Peristaltic Pumps
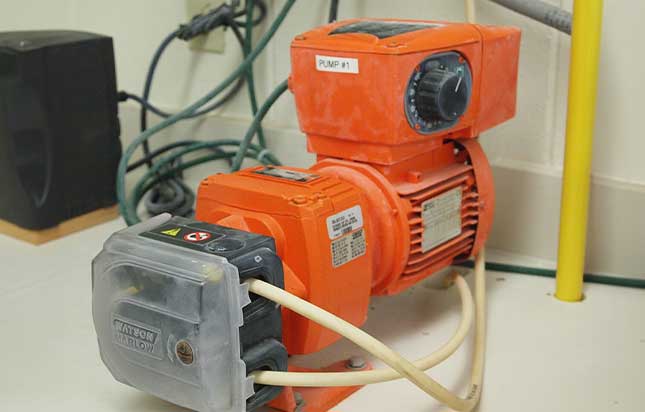
Source: Wikipedia
Peristaltic pumps work by compressing a flexible tube with rotating rollers, which pushes the liquid through.
They’re great for handling viscous or shear-sensitive fluids, such as gels or pastes, and are often used in food, pharmaceuticals, and laboratory settings.
Piston Pumps
Piston pumps operate by moving a piston back and forth within a cylinder, forcing liquid in and out.
These pumps are very precise and are often used in applications requiring high pressure, like in oil and gas industries.
Solenoid Pumps
Solenoid pumps use an electromagnetic solenoid coil to move a diaphragm, which draws and expels liquid.
They are compact, simple, and suitable for low-flow applications like aquarium maintenance or small-scale chemical dosing.
Hydraulic Pumps
These pumps rely on hydraulic pressure to move the diaphragm, allowing them to handle higher flow rates.
Hydraulic pumps are often used in industrial applications where larger volumes are needed.
What are the Benefits to Using a Dosing Pump?
Using a dosing pump offers numerous benefits across various industries, making them a crucial component in fluid management.
Precision
One of the primary advantages of dosing pumps is their ability to deliver precise amounts of liquid.
This accuracy ensures that the correct concentrations of chemicals, nutrients, or additives are consistently applied, which is essential for maintaining product quality and compliance with regulatory standards.
Automation
Dosing pumps can be automated, reducing the need for manual intervention.
This automation streamlines processes, enhances efficiency, and minimises the risk of human error, leading to improved operational reliability.
Safety
Dosing pumps improve safety by minimising direct contact with hazardous chemicals.
By accurately controlling chemical dosing, these pumps help prevent over-application, reducing the risk of accidents and exposure to harmful substances.
Consistency
Dosing pumps provide consistent results, maintaining stable concentrations over time.
This reliability is vital in processes like water treatment, food production, and pharmaceuticals, where variations can lead to quality issues.
Versatility
Dosing pumps are versatile and can handle a wide range of fluids, including corrosive or viscous liquids.
Their adaptability makes them suitable for various applications across different industries.
Cost-Effectiveness
By reducing waste and optimising chemical usage, dosing pumps contribute to cost savings.
Their efficiency in fluid management helps lower operational costs over time, making them a valuable investment.
What are the Limitations of Using a Dosing Pump?
While dosing pumps offer many advantages, they also have certain limitations that can impact their effectiveness in various applications.
Cost
One of the primary limitations of dosing pumps is their initial cost.
High-quality dosing pumps can be expensive to purchase and install, which may deter some small businesses from utilising them.
Maintenance Requirements
Dosing pumps require regular maintenance to ensure optimal performance and accuracy.
This can include cleaning, calibration, and replacing worn parts.
Neglecting maintenance can lead to dosing errors, which may affect process quality.
Clogging Issues
Some dosing pumps can be prone to clogging, especially when handling viscous fluids or those containing solid particles.
Clogs can disrupt the flow and require frequent cleaning or filtration solutions, adding to maintenance costs and downtime.
Pressure Sensitivity
Certain dosing pumps may have limitations in handling high-pressure applications.
If a system’s pressure exceeds the pump’s specifications, it could lead to failures or inaccuracies in dosing.
Limited Flow Rates
Dosing pumps are typically designed for low to moderate flow rates, making them unsuitable for high-volume applications.
This limitation can restrict their use in processes requiring large quantities of liquid to be delivered quickly.
Fluid Compatibility
Not all dosing pumps can handle every type of fluid, particularly aggressive or corrosive substances.
Ensuring compatibility between the pump materials and the fluid being dosed is crucial to prevent damage and maintain efficiency.
What are the Alternatives to Using a Dosing Pump?
In some applications, alternatives to dosing pumps may be more suitable, depending on specific needs and requirements.
Here are several alternatives:
Gravity Feed Systems
Gravity feed systems rely on the natural flow of liquid from a higher elevation to a lower one.
They are simple and cost-effective but lack the precision of dosing pumps.
These systems are best for applications where exact measurements are not critical.
Hand Pumps
Hand pumps are manually operated devices that can be used for small-scale chemical dosing.
While they are low-cost and portable, hand pumps require human intervention, making them less efficient for large or continuous applications.
Metering Valves
Metering valves allow for controlled fluid flow through manual adjustment.
While they can provide some level of accuracy, they don’t offer the automation or precision found in dosing pumps.
Metering valves are often used in conjunction with other pumping systems for better control.
Flow-Controlled Pumps
Flow-controlled pumps automatically adjust flow rates based on system conditions.
They are useful for maintaining steady flow but may not provide the precise dosing capabilities needed in specific chemical applications.
Peristaltic Tubing Systems
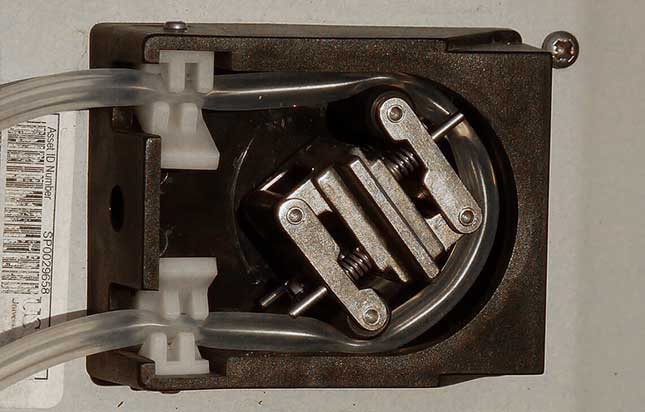
Source: Wikipedia
Simple peristaltic tubing setups can move liquids but lack the advanced control and accuracy of dedicated dosing pumps.
These systems are suitable for low-tech applications but may not meet all dosing needs.
Conclusion
You should now have an understanding of dosing pumps and how they work.
Dosing pumps play a crucial role in applications requiring precise fluid control.
They allow for the accurate addition of chemicals, nutrients, and other fluids across industries such as water treatment, agriculture, and manufacturing.
While dosing pumps offer benefits like precision, automation, and safety, they also come with limitations, such as cost and maintenance requirements.
Understanding the various types of dosing pumps and how they work helps users choose the right pump for specific needs.
Additionally, alternatives like gravity feed systems and metering valves may be suitable for applications where precision dosing isn’t critical.
However, when accuracy, consistency, and control are required, dosing pumps remain unmatched.
With the right selection and setup, dosing pumps provide an effective, efficient solution for precise fluid management in both industrial and small-scale settings.
For more information, or advice on any of your pump needs, get in contact with us here at KD Pumps.
Comments are closed.