How Do Centrifugal Pumps Work?
A centrifugal pump utilises the transfer of rotational energy from one or more impellers to move fluid mechanically.
The impellers, which are driven rotors, rapidly rotate, and fluid enters along their axis.
The centrifugal force then propels the fluid through the vane tips of the impeller along its circumference, increasing its velocity and pressure and directing it towards the pump outlet.
The pump casing is designed to restrict the fluid flow from the inlet, guide it into the impeller, and regulate its speed and direction before discharge.
In the following chapters, we further explore how centrifugal pumps work and where they’re typically found.
Article Chapters
How Centrifugal Pumps Work
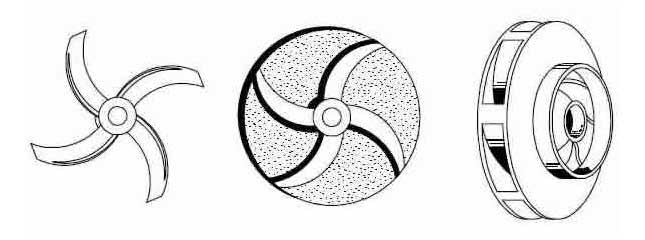
3 Types of Impeller. Image credit: Engineers Edge
The primary element of a centrifugal pump is the impeller, which comprises a set of curved blades.
In an enclosed impeller, these blades are usually enclosed between two discs.
For fluids that contain solid particles, an open or semi-open impeller (with only one disc as support) is preferred.
The fluid is introduced to the impeller through its axis or the “eye,” and exits the impeller through the space between its vanes located at the circumference.
The impeller is mounted on a drive shaft that is connected to a motor and is rotated at high speeds ranging from 500 to 5000 rpms.
As the impeller rotates, it imparts kinetic energy to the fluid, accelerating it out through the vanes and into the pump casing.
Types of Pump Casings
Volute Case Design
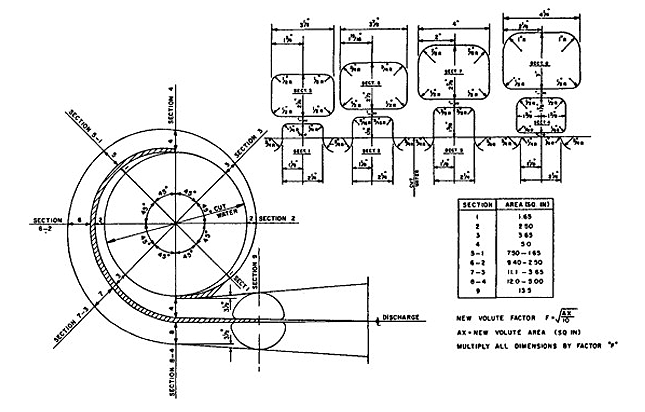
Volute Case Design. Image credit: Science Direct
There are two fundamental designs of pump casing, namely the volute and diffuser.
Both designs aim to convert the fluid flow into a regulated discharge at pressure.
A volute casing features an offset impeller that creates a curved funnel with a growing cross-sectional area towards the pump outlet.
This arrangement leads to a rise in fluid pressure towards the outlet.
Diffuser Case Design
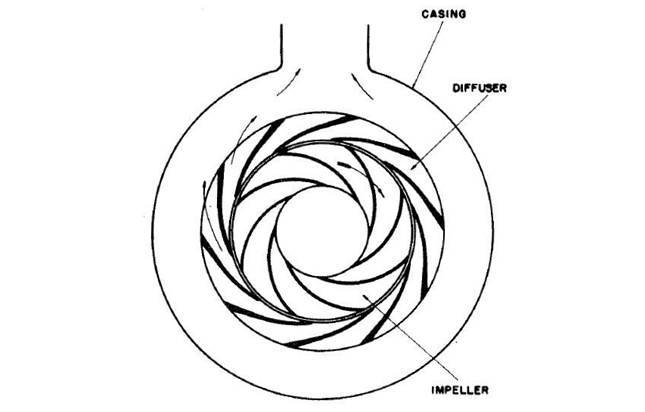
Diffuser Case Design. Image credit: Intro to Pumps
Diffuser designs of pump casing follow the same principle as volute designs, but they work by increasing the fluid pressure as the fluid is expelled between a set of stationary vanes surrounding the impeller.
These designs can be customized for specific applications and can be more efficient.
On the other hand, volute cases are better suited for applications that involve entrained solids or high viscosity fluids, where it’s advantageous to avoid the added constrictions of diffuser vanes.
However, the asymmetry of the volute design can result in greater wear on the impeller and drive shaft.
Limitations of Centrifugal Pumps
A centrifugal pump operates efficiently when its impeller rotates constantly at high speeds.
However, its efficiency reduces with high viscosity fluids as they create more resistance and require higher pressure to maintain a specific flow rate.
Generally, centrifugal pumps are best suited for low-pressure, high-capacity liquid pumping applications with viscosities ranging from 0.1 to 200 cP.
Excessive wear and overheating, leading to damage and premature failures, can be caused by slurries such as mud or high viscosity oils when they are pumped using centrifugal pumps.
To avoid such problems, positive displacement pumps, which often operate at considerably lower speeds, are preferred.
In addition, pumped media that are sensitive to shearing, such as emulsions, slurries, or biological liquids, can be damaged by the high speed of a centrifugal pump’s impeller.
In these cases, a positive displacement pump’s lower speed is preferred.
A centrifugal pump has some limitations compared to a positive displacement pump.
Firstly, it requires priming with the pumped fluid and cannot provide suction when dry.
Therefore, it’s not suitable for intermittent supply applications.
Secondly, if the feed pressure varies, a centrifugal pump will produce a variable flow, while a positive displacement pump is insensitive to changing pressures and provides a constant output.
Therefore, for applications where accurate dosing is necessary, a positive displacement pump is preferred.
Where are Centrifugal Pumps Usually Found?
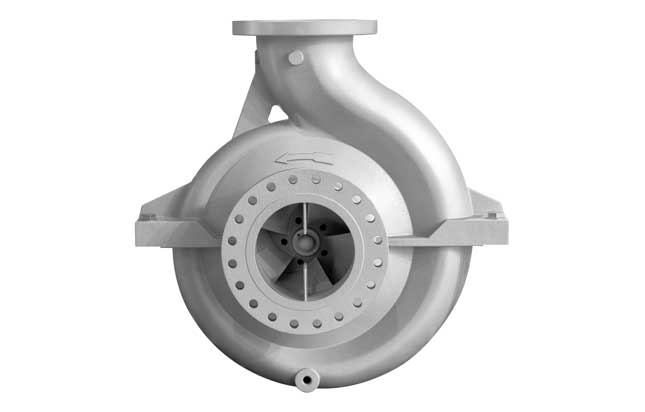
Cross Section Impeller Inside Centrifugal Pump. Image credit: Shutterstock
Centrifugal pumps are utilised in industrial, agricultural, and domestic applications for pumping water, solvents, organics, oils, acids, bases, and other low viscosity liquids.
With a design suitable for nearly any application, centrifugal pumps are seen as a very versatile option.
Conclusion
A centrifugal pump is a device that transfers rotational energy from impellers to fluids, increasing their velocity and pressure and directing them towards the pump outlet.
This simplicity results in easy operation and maintenance.
Centrifugal pump designs provide affordable and uncomplicated solutions for low pressure, high capacity pumping applications that involve low viscosity fluids like solvents, water, light oils, and chemicals.
These pumps are often used in water supply and circulation, irrigation, and chemical transfer in petrochemical plants.
On the other hand, positive displacement pumps are more suitable for high-pressure applications involving highly viscous fluids like thick oils and slurries.
They are also preferred for complex feeds such as foodstuffs or biological fluids, and when precise dosing is necessary.
Comments are closed.