What is a Positive Displacement Pump?
In the world of fluid mechanics, pumps play a crucial role in moving liquids or gases from one place to another.
Among various types of pumps, the positive displacement pump stands out for its unique characteristics and applications.
But exactly is a positive displacement pump?
This article explores what a positive displacement pump is, how it works, its types, benefits, limitations, and alternatives to positive displacement pumps.
Article Chapters
What is a Positive Displacement Pump?
A positive displacement pump is a type of pump that moves fluid by trapping a fixed amount of it and then forcing it into a discharge pipe.
Unlike centrifugal pumps, which rely on kinetic energy to propel fluid, positive displacement pumps operate by repeatedly trapping and releasing fluid through a mechanical or diaphragm action.
This method ensures a consistent flow rate regardless of changes in discharge pressure, making them ideal for applications where precise fluid control is crucial.
These pumps are characterised by their ability to deliver a steady flow of fluid at varying pressures, making them suitable for tasks such as metering, dosing, and transferring viscous fluids.
Positive displacement pumps can handle a wide range of fluids, from thin, water-like substances to thick, viscous materials that may challenge other pump types.
Their versatility extends their use across various industries including oil and gas, chemical processing, food and beverage, pharmaceuticals, and wastewater management.
The mechanisms of positive displacement pumps vary, including reciprocating, rotary, and peristaltic designs, each offering unique benefits depending on the specific requirements of the application.
What are the Different Types of Positive Displacement Pump?
Positive displacement pumps come in various types, each designed to suit different fluid handling needs and operational requirements.
Here are the main types of positive displacement pumps:
Reciprocating Pumps
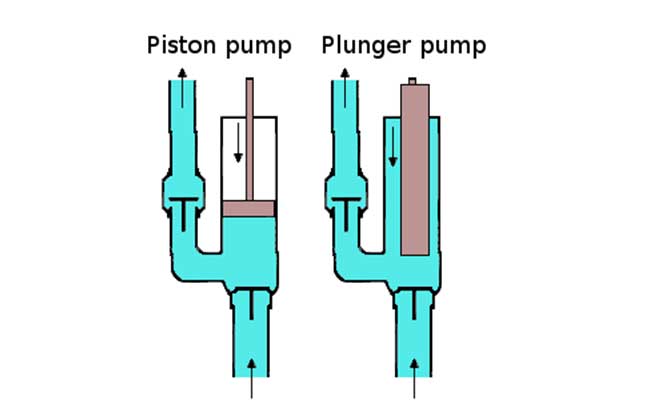
Source: Wikipedia
Reciprocating pumps use a piston, plunger, or diaphragm to create a reciprocating motion within a cylinder.
As the piston or plunger moves back and forth, it alternately draws in and expels fluid through inlet and outlet valves.
These pumps are known for their ability to handle high-pressure applications and are often used in processes requiring precise metering or dosing of fluids.
Examples include metering pumps used in chemical dosing systems and high-pressure cleaning systems.
Rotary Pumps
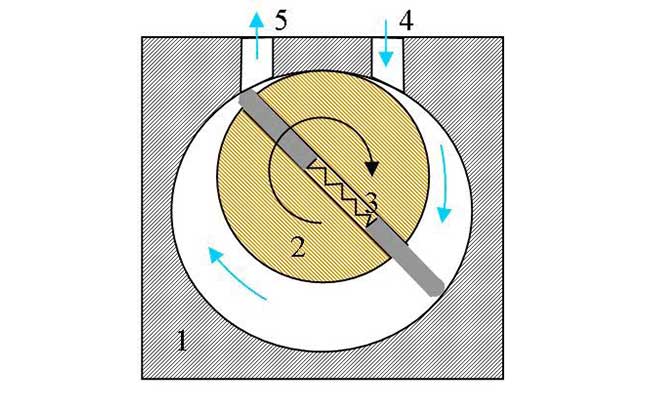
Source: Wikipedia
Rotary pumps operate by rotating an element within a casing to create suction and discharge actions.
Common types of rotary pumps include:
Gear Pumps
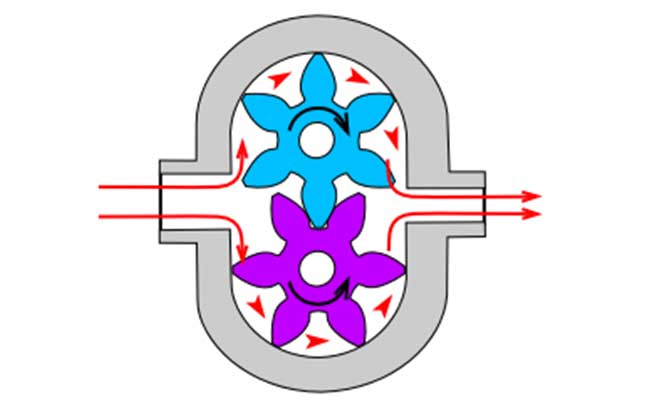
Source: Wikipedia
Use intermeshing gears to trap and transfer fluid from the inlet to the outlet. They are reliable for transferring viscous fluids like oils and fuels.
Vane Pumps
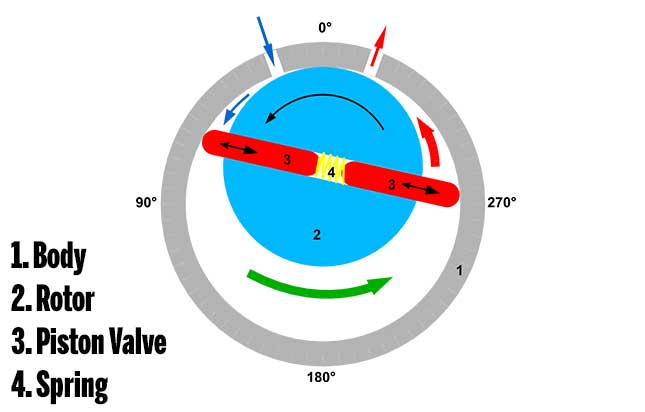
Source: Wikipedia
Feature sliding vanes that create chambers between the vanes and casing, trapping and displacing fluid as the rotor rotates.
Vane pumps are suitable for medium-viscosity liquids and are often used in hydraulic systems.
Screw Pumps
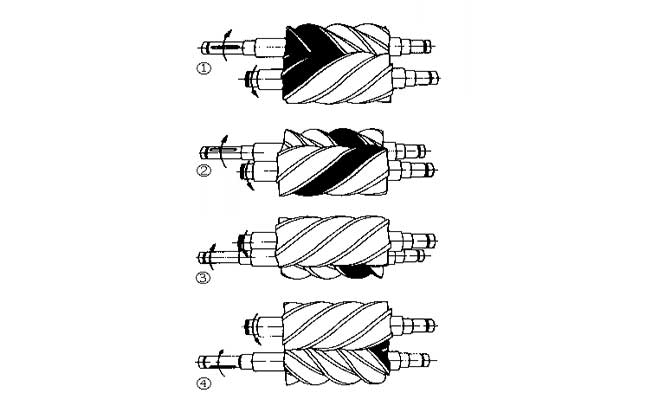
Source: Wikipedia
Use rotating screws to trap and move fluid along the screw threads within the pump casing.
Screw pumps are capable of handling high viscosity fluids and are used in industrial applications such as oil refineries and wastewater treatment plants.
Diaphragm Pumps
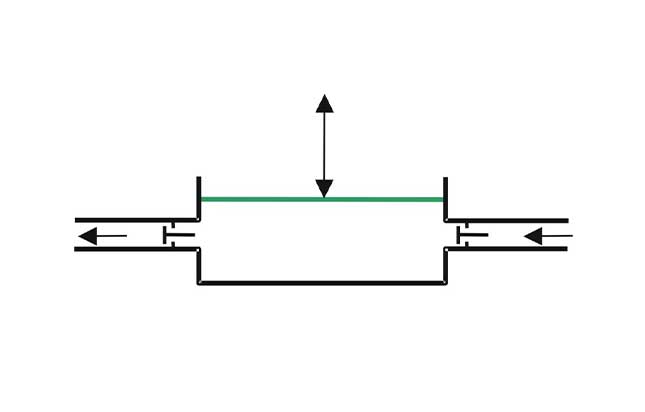
Source: Wikipedia
Diaphragm pumps use a flexible diaphragm that moves back and forth to create suction and discharge cycles.
The diaphragm flexes to draw fluid into the pump chamber and then pushes it out through the discharge port.
These pumps are valued for their ability to handle abrasive or corrosive fluids without contaminating the environment.
They are commonly used in chemical processing, wastewater treatment, and mining operations.
Peristaltic Pumps
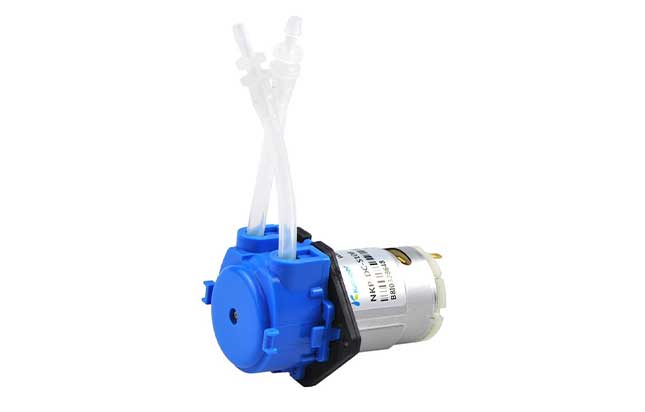
Source: Amazon
Peristaltic pumps operate by squeezing a flexible tube or hose to create a vacuum that draws fluid into the tube and then propels it forward.
The squeezing action is typically achieved by rollers or shoes that compress the tube sequentially, pushing the fluid through.
Peristaltic pumps are ideal for pumping delicate or shear-sensitive fluids such as pharmaceuticals, food products, and biological materials.
What are the Benefits of a Positive Displacement Pump?
Positive displacement pumps offer several benefits that make them advantageous for various industrial and commercial applications:
Precise Flow Control
One of the primary advantages of positive displacement pumps is their ability to provide accurate and consistent flow rates.
Unlike centrifugal pumps, which vary flow rate based on pressure changes, positive displacement pumps deliver a fixed volume of fluid per cycle, making them ideal for applications requiring precise metering or dosing of liquids.
Suitability for Viscous Fluids
Positive displacement pumps are well-suited for handling viscous fluids that may challenge other pump types.
Their mechanism of trapping and displacing fluid allows them to move thick or sticky liquids effectively without losing efficiency or performance.
Self-Priming Capability
Many positive displacement pumps are self-priming, meaning they can evacuate air from the suction line and create a vacuum to draw fluid into the pump.
This feature eliminates the need for manual priming and ensures continuous operation even when there is air in the fluid being pumped.
High Pressure Capability
Certain types of positive displacement pumps, such as reciprocating and screw pumps, are capable of generating high discharge pressures.
This makes them suitable for applications requiring pumping against high head pressures or overcoming friction losses in long pipelines.
Handling of Abrasive and Corrosive Fluids
Positive displacement pumps, especially diaphragm and peristaltic pumps, are designed to handle abrasive, corrosive, or shear-sensitive fluids without contaminating the pump or the environment.
This makes them ideal for chemical processing, mining, and wastewater treatment applications where fluid compatibility is critical.
Versatility
Positive displacement pumps come in various configurations and can be adapted to a wide range of operating conditions and fluid types.
This versatility allows them to be used in diverse industries such as oil and gas, food and beverage, pharmaceuticals, and manufacturing.
What are the Limitations to a Positive Displacement Pump?
While positive displacement pumps offer several advantages, they also have limitations that should be considered depending on the application:
Viscosity Sensitivity
Positive displacement pumps can experience reduced efficiency or require modifications when handling fluids with significantly varying viscosities.
High-viscosity fluids may increase resistance within the pump, affecting performance and requiring higher operating pressures.
Temperature Sensitivity
Some types of positive displacement pumps, particularly those with elastomeric components like diaphragm or peristaltic pumps, may be sensitive to temperature extremes.
High temperatures can degrade elastomers and affect pump performance, while low temperatures can cause stiffness or reduced flexibility, impacting the pump’s ability to operate smoothly.
Maintenance Requirements
Positive displacement pumps often require regular maintenance due to the wear and tear of moving parts, seals, and valves.
Maintenance tasks may include lubrication, inspection of seals, and periodic replacement of wearing components to ensure continued reliability and efficiency.
Pressure Limitations
While certain types of positive displacement pumps can generate high pressures, they may have limitations compared to centrifugal pumps in terms of handling very high discharge pressures or large flow rates.
The design and construction of the pump must match the application’s pressure requirements to avoid potential issues such as leakage or pump failure.
Cavitation Risk
Reciprocating and rotary positive displacement pumps can be susceptible to cavitation under certain conditions, especially if the suction pressure is too low or the fluid viscosity changes abruptly.
Cavitation can cause damage to pump components and reduce efficiency, necessitating careful monitoring of operating conditions.
Size and Weight
Positive displacement pumps, especially those designed for high-pressure or high-flow applications, can be larger and heavier compared to centrifugal pumps of similar capacity.
This can impact installation space requirements and transportation logistics, particularly in compact or mobile equipment designs.
What are the Alternatives to a Positive Displacement Pump?
In applications where positive displacement pumps may not be suitable, several alternative pump types offer different operating principles and capabilities:
Centrifugal Pumps
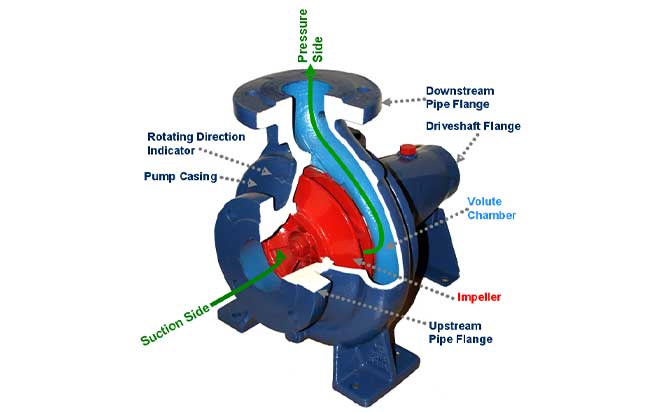
Source: Wikipedia
Centrifugal pumps operate by converting rotational energy from an impeller into kinetic energy to move fluid.
They are ideal for applications requiring high flow rates and moderate pressure, such as water circulation, HVAC systems, and wastewater treatment.
Centrifugal pumps are less effective for handling viscous fluids or applications requiring precise flow control.
Air-Operated Double Diaphragm (AODD) Pumps
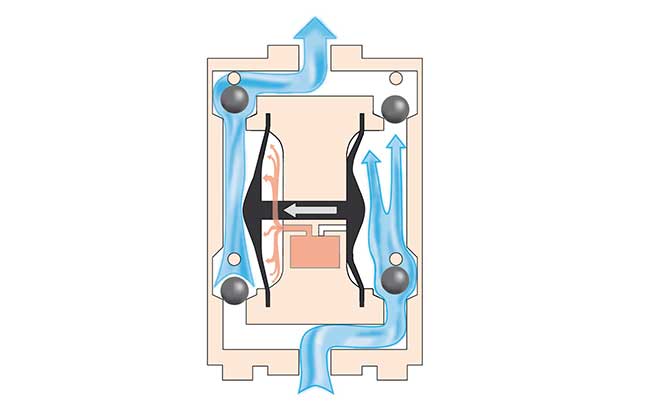
Source: Wikipedia
AODD pumps use compressed air to alternately expand and contract diaphragms, creating suction and discharge cycles.
They are versatile for handling abrasive, viscous, and shear-sensitive fluids in industries like chemicals, food processing, and mining.
AODD pumps are self-priming and can run dry without damage, but they may require significant air consumption and maintenance.
Submersible Pumps
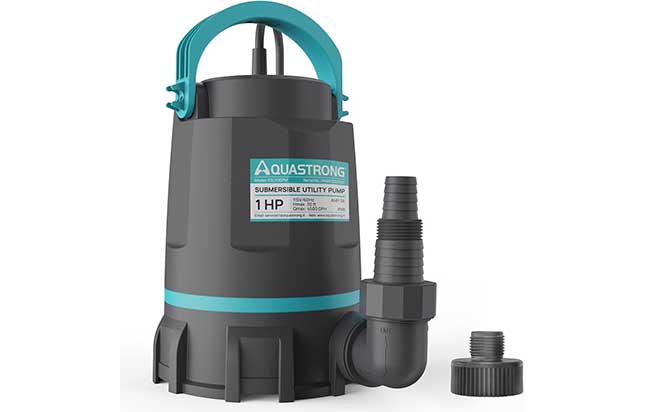
Source: Amazon
Submersible pumps are immersed in the fluid they pump, typically used for drainage, sewage, and groundwater applications.
They are designed to handle solids and slurries, making them suitable for harsh environments like construction sites and municipal wastewater systems.
Submersible pumps vary in size and capacity to accommodate different fluid levels and flow requirements.
Jet Pumps
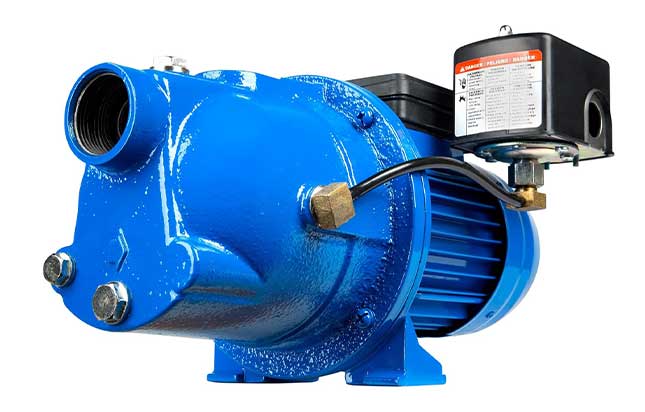
Source: Amazon
Jet pumps use fluid flow (liquid or gas) to create a vacuum that draws fluid into the pump and propels it through a discharge outlet.
They are commonly used in wells and boreholes for lifting water to the surface and are versatile for various water supply and irrigation applications.
Conclusion
Positive displacement pumps play a vital role in industries where precise fluid control and consistent performance are critical.
They offer unique benefits such as accurate flow control and self-priming capabilities but come with limitations like viscosity sensitivity and higher maintenance needs.
Understanding their operation and choosing the right type of positive displacement pump for specific applications can optimise efficiency and ensure reliable fluid handling processes.
As technology advances, these pumps continue to evolve, adapting to the changing demands of modern industries while maintaining their essential role in fluid mechanics.
Comments are closed.