What is a Progressive Cavity Pump?
Pumps play a crucial role in many industries.
They move fluids from one place to another.
Among the various types, the progressive cavity pump stands out.
This pump is known for its ability to handle viscous fluids and solids.
In this article, we will explore what a progressive cavity pump is, how it works, its uses, advantages, disadvantages, and alternatives.
Article Chapters
What is a Progressive Cavity Pump?
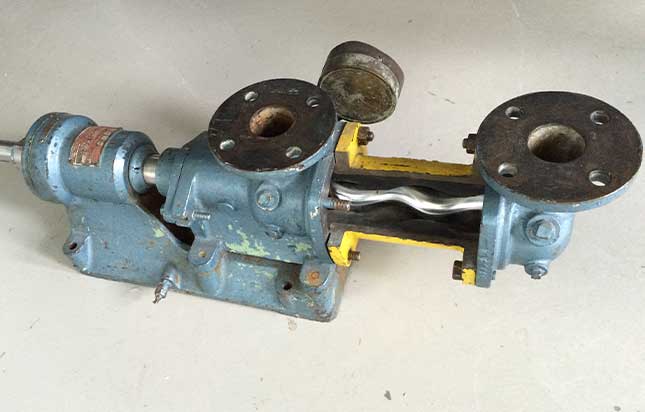
Source: Wikipedia
A progressive cavity pump is a type of positive displacement pump, also known as a helical rotor pump or eccentric screw pump.
It is designed to handle a wide range of fluids, including those that are thick, viscous, or contain solids.
This pump is particularly valued in industries that require the reliable movement of challenging substances.
The core components of a progressive cavity pump are the rotor and the stator.
The rotor is typically made of metal and has a helical shape, similar to a twisted screw.
The stator, which encases the rotor, is usually made from a flexible material like rubber and has a matching helical internal shape.
As the rotor turns inside the stator, it creates a series of sealed cavities that move the fluid through the pump in a smooth, continuous flow.
The design of the progressive cavity pump allows it to handle fluids that other pumps might struggle with.
For example, it can easily pump high-viscosity fluids such as molasses, slurries, and thick oils.
It can also handle fluids containing solids, like wastewater sludge or food products with particulates, without clogging or damaging the pump.
How Does a Progressive Cavity Pump Work?
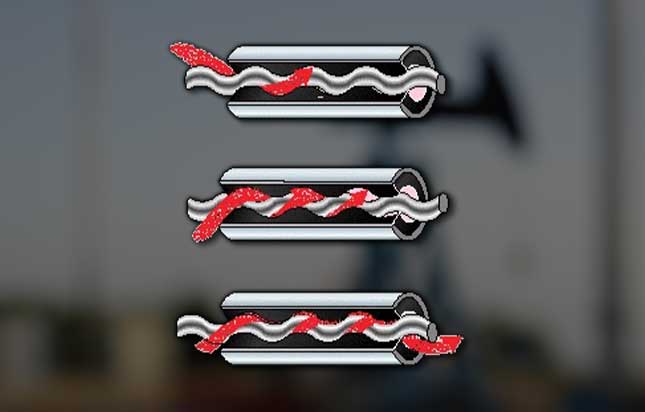
Source: Wikipedia
A progressive cavity pump operates based on the interaction between a helical rotor and a matching stator.
This design creates a series of sealed cavities that move the fluid through the pump in a continuous, non-pulsating flow.
Here’s a step-by-step explanation of how a progressive cavity pump works:
Rotor and Stator Interaction
The rotor, typically made of metal and shaped like a twisted screw, rotates inside the stator, which is usually made of a flexible material like rubber.
The stator has a helical internal shape that matches the rotor.
Formation of Cavities
As the rotor turns, it creates cavities between the rotor and the stator.
These cavities are sealed due to the close fit of the rotor inside the stator.
Cavity Movement
When the rotor rotates, the cavities move along the length of the pump.
New cavities are continuously formed at the inlet as the existing ones move towards the outlet.
Fluid Transport
The fluid enters the pump through the inlet and gets trapped in the cavities.
As the rotor continues to turn, the cavities move towards the outlet, carrying the fluid along with them.
Continuous Flow
The movement of the cavities ensures a smooth, continuous flow of fluid.
This non-pulsating flow is ideal for applications that require consistent pressure and minimal fluid agitation.
What are Progressive Cavity Pumps Used For?
Progressive cavity pumps are versatile and find applications across various industries due to their ability to handle a wide range of fluids, including those that are viscous, abrasive, or contain solids.
Here are some common uses of progressive cavity pumps:
Oil and Gas Industry
Progressive cavity pumps are widely used in the oil and gas sector for pumping crude oil, drilling mud, and various other fluids encountered during exploration and production operations.
Their ability to handle viscous and abrasive fluids makes them ideal for these applications.
Food and Beverage Processing
In the food and beverage industry, progressive cavity pumps are used for pumping thick and viscous fluids such as syrups, chocolate, sauces, and pastes.
They are also used in handling delicate food products containing solids, like fruit purees and mashed vegetables.
Wastewater Treatment
Progressive cavity pumps play a crucial role in wastewater treatment plants for pumping sludge, grit, and other abrasive materials.
They can handle high-viscosity fluids and fluids containing solids without clogging, making them suitable for these demanding applications.
Chemical Processing
In chemical plants, progressive cavity pumps are used for transferring various chemicals, acids, and corrosive fluids.
Their ability to provide a smooth and consistent flow makes them suitable for metering and dosing applications where accuracy is essential.
Mining Industry
Progressive cavity pumps are employed in the mining industry for pumping slurry, tailings, and abrasive materials.
They can handle high concentrations of solids and provide reliable performance in harsh mining environments.
Water and Wastewater Management
Progressive cavity pumps are used in water and wastewater management systems for pumping sewage, sludge, and industrial wastewater.
Their ability to handle variable flow rates and viscous fluids makes them suitable for these applications.
The Advantages of Progressive Cavity Pumps
Progressive cavity pumps offer several advantages that make them a preferred choice for many industrial applications.
Here are some of the key benefits:
Handles Viscous Fluids
Progressive cavity pumps excel at pumping thick, viscous fluids that other pumps may struggle with.
This includes substances like sludge, molasses, adhesives, and heavy oils.
Can Pump Solids
One of the most significant advantages of progressive cavity pumps is their ability to handle fluids containing solids.
The design of the pump allows it to move materials like sewage sludge, wastewater grit, and food products with particulates without clogging or damage.
Smooth Flow
Progressive cavity pumps provide a continuous, non-pulsating flow of fluid.
This smooth flow is ideal for applications that require precise metering or where pulsations could damage sensitive equipment downstream.
Low Shear
These pumps are gentle on the fluid being pumped, making them suitable for handling shear-sensitive materials like polymers, shear-thinning fluids, and delicate food products.
Self-Priming
Progressive cavity pumps are self-priming, meaning they can start pumping without the need to be filled with fluid first.
This feature makes them easy to use and reduces the risk of dry running.
High Pressure
Progressive cavity pumps can generate high discharge pressures, making them suitable for applications that require pumping over long distances or against high heads.
Versatility
These pumps can handle a wide range of fluids and applications, making them versatile and adaptable to various industries and processes.
Efficient Operation
Progressive cavity pumps are energy-efficient, requiring less power to operate compared to some other types of pumps.
This can result in cost savings over the long term.
The Disadvantages of Progressive Cavity Pumps
While progressive cavity pumps offer numerous advantages, they also come with some disadvantages that should be considered when selecting a pump for a specific application.
Here are some of the main drawbacks of progressive cavity pumps:
Complex Design
Progressive cavity pumps have a more complex design compared to some other types of pumps.
This complexity can make them more challenging to maintain and repair, requiring specialised knowledge and skills.
Wear and Tear
The rotor and stator components of progressive cavity pumps are subject to wear over time, especially when pumping abrasive fluids or those containing solids.
This wear can lead to reduced pump efficiency and increased maintenance requirements.
Cost
Progressive cavity pumps tend to be more expensive to purchase upfront compared to simpler pump designs like centrifugal pumps.
Additionally, ongoing maintenance and repair costs can be higher due to the need for replacement parts and specialised service.
Size
Progressive cavity pumps can be larger and heavier than other types of pumps, making them less suitable for applications where space is limited or where portability is required.
Sensitivity to Dry Running
Running a progressive cavity pump dry, meaning without fluid, can cause damage to the rotor and stator components.
It’s essential to ensure that the pump is always adequately primed before starting it to avoid this issue.
Progressive Cavity Pump Alternatives
While progressive cavity pumps offer unique advantages, they may not be the best choice for every application.
Several alternative pump types are available, each with its own set of benefits and limitations.
Here are some common alternatives to progressive cavity pumps:
Centrifugal Pumps
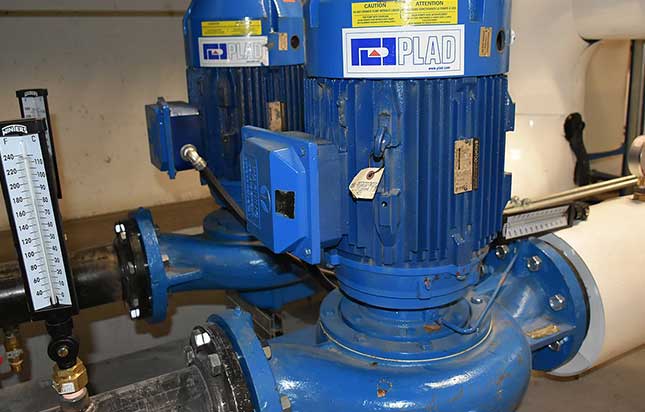
Source: Wikipedia
Centrifugal pumps are widely used in various industries for their simplicity and efficiency.
They work by converting rotational energy into kinetic energy to move fluids.
Centrifugal pumps are suitable for pumping low-viscosity fluids over long distances or to high elevations.
However, they are less effective for handling viscous fluids or those containing solids.
Diaphragm Pumps
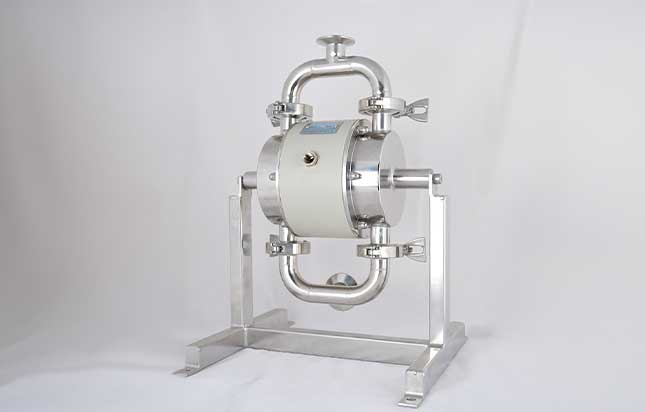
Source: Wikipedia
Diaphragm pumps use a flexible diaphragm to create a pumping action.
They are capable of handling abrasive and viscous fluids, making them suitable for applications where progressive cavity pumps may struggle.
Diaphragm pumps can also run dry without damage, making them ideal for intermittent duty cycles.
However, they may produce pulsating flow, which can be undesirable in some applications.
Peristaltic Pumps
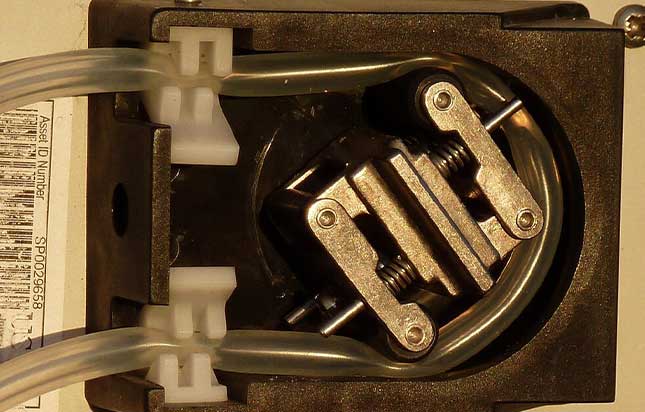
Source: Wikipedia
Peristaltic pumps utilise rotating rollers to compress a flexible tube, creating a pumping action.
They are gentle on the fluid being pumped and can handle shear-sensitive materials effectively.
Peristaltic pumps are commonly used in laboratory settings, pharmaceutical manufacturing, and food and beverage processing.
However, they are limited in terms of pressure and flow rate compared to other pump types.
Gear Pumps
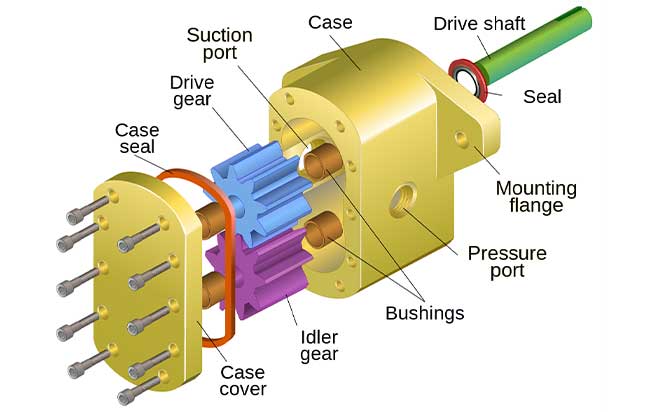
Source: Wikipedia
Gear pumps consist of two or more interlocking gears that create a pumping action.
They are suitable for pumping viscous fluids and can provide a smooth, continuous flow.
Gear pumps are commonly used in hydraulic systems, lubrication systems, and chemical processing.
However, they may not handle solids as effectively as progressive cavity pumps.
Lobe Pumps
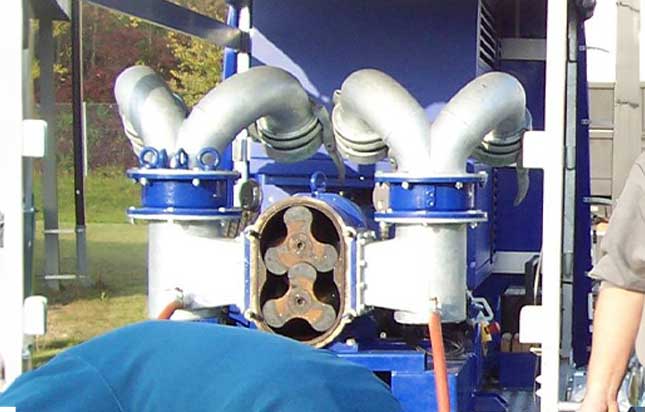
Source: Wikipedia
Lobe pumps use two rotating lobes to move fluid through the pump.
They are capable of handling viscous fluids and those containing solids, making them suitable for applications where progressive cavity pumps are used.
Lobe pumps are commonly used in hygienic applications such as food processing and pharmaceutical manufacturing.
However, they can be more expensive and complex than other pump types.
Conclusion
Progressive cavity pumps are a versatile and reliable option for handling viscous fluids, solids-laden slurries, and abrasive materials across various industries.
Their unique design allows for smooth, consistent flow and efficient operation, making them ideal for challenging pumping applications.
While they have some disadvantages, such as complexity and maintenance requirements, their advantages often outweigh these drawbacks.
Additionally, there are alternative pump types available to suit specific needs and preferences.
Ultimately, the selection of a pump should be based on careful consideration of factors such as fluid properties, application requirements, and budget constraints.
For more information, or if you require help with pumps, get in touch with us here at KD Pumps.
Comments are closed.